In today’s competitive market, consistency and precision are paramount. This holds especially true in the food, pharmaceutical, and chemical industries, where the packaging of granular products must be precise to meet both regulatory standards and consumer expectations. Granule packaging machines play a pivotal role in ensuring that each package contains the correct amount of product. But how do these machines ensure accuracy in weight and volume? The answer lies in advanced technology and meticulous design features that work in tandem to achieve reliable, repeatable results.
The Mechanics Behind Accurate Packaging
At the heart of any granule packaging machine is a system designed to measure and control the amount of product that is dispensed into each package. The process typically involves the following steps:
Product Feeding and Flow Control
The granules enter the packaging system through a hopper or feeder, which is equipped to regulate the flow of product. Depending on the machine’s design, different types of feeders—such as auger feeders, vibratory feeders, or rotary feeders—are employed. These feeders are designed to handle the specific characteristics of the granules, such as size, shape, and flowability. The goal is to ensure that the granules flow smoothly into the measuring unit without clumping or spilling.
Weighing Mechanism
Granule packaging machines typically employ electronic or mechanical weighers to monitor and control the weight of the product being dispensed. Electronic weighers are equipped with load cells that can detect minute changes in weight, providing highly accurate readings in real time. As granules move toward the packaging area, the machine continually measures their weight, ensuring that only the desired amount enters the package. This precision ensures that each package contains the correct weight, reducing the risk of overfilling or underfilling.
Volume Measurement and Control
In some applications, particularly in cases where the granules are free-flowing and homogenous, volume-based control may be employed instead of weight. Volume-based packaging uses mechanisms like augers or volumetric cups to precisely measure the amount of product dispensed into each package. These systems are calibrated to handle specific product densities, ensuring consistency in the volume of granules, even when the density or flow characteristics of the granules change.
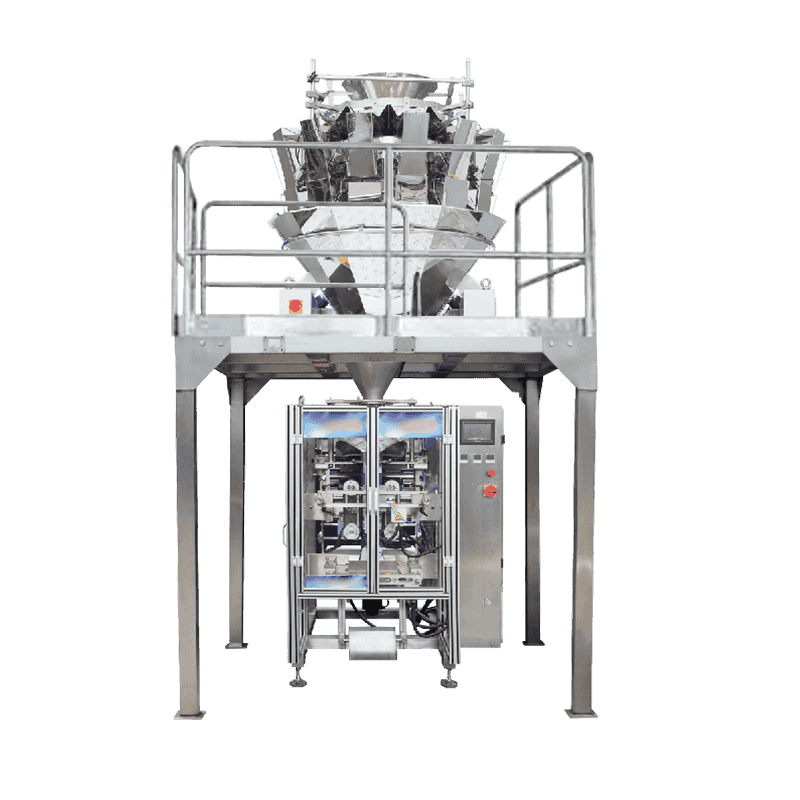
Adjustment and Calibration
Granule packaging machines are equipped with advanced sensors that allow for real-time adjustments. If a discrepancy is detected between the target weight or volume and the actual amount being dispensed, the system can automatically adjust the flow rate or dispensing speed. This dynamic recalibration ensures that each package adheres to strict specifications without human intervention. Additionally, many machines allow for manual calibration to further enhance precision, especially when switching between different product types or package sizes.
Sealing and Final Verification
Once the granules are dispensed and the weight or volume has been confirmed, the package is sealed and sent through a final verification process. Many packaging machines incorporate automatic checkweighers that inspect the weight of each package before it is sealed. Any packages that fall outside the acceptable weight range are rejected, ensuring that only correctly filled packages reach the consumer. This final step enhances quality control and helps maintain compliance with industry regulations.
The Importance of Precision in Granule Packaging
The ability to control the weight or volume of granules in each package is not just a technical requirement; it is a business necessity. For manufacturers, precision in packaging is crucial for several reasons:
Regulatory Compliance: Packaging regulations often require that products meet specific weight or volume criteria. Overfilled or underfilled packages can result in costly fines or regulatory action.
Consumer Trust: Inconsistent package content can erode consumer trust. Consumers expect to receive the correct amount of product, and any deviation can lead to dissatisfaction and lost sales.
Cost Efficiency: Accurately controlled packaging reduces product waste. Overfilling packages wastes material, while underfilling packages results in lost revenue. Optimizing packaging precision helps manufacturers achieve maximum cost efficiency.
Contact Us