The Magic Behind Liquid Filling Machines
In the world of manufacturing and packaging, precision is everything. Whether it’s a bottle of soda, a vial of medicine, or a container of motor oil, ensuring that each product is filled accurately and consistently is crucial. This is where liquid filling machines come into play. These ingenious devices are the unsung heroes behind countless products we use every day, quietly working to ensure efficiency, accuracy, and hygiene in production lines around the globe.
Liquid filling machines are specialized equipment designed to transfer precise amounts of liquid into containers. They may seem straightforward at first glance, but their inner workings are a fascinating blend of engineering and innovation. From small-scale operations to high-speed industrial lines, these machines adapt to meet diverse needs, making them indispensable across industries like food and beverage, pharmaceuticals, cosmetics, and chemicals.
How Do Liquid Filling Machines Work?
At their core, liquid filling machines operate on principles of fluid dynamics, mechanics, and automation. The process begins with a reservoir that holds the liquid to be dispensed. Depending on the type of machine, the liquid is then measured and transferred into containers through various mechanisms such as pistons, gravity, vacuum, or pumps.
One common method involves using volumetric fillers, which measure exact volumes of liquid before releasing them into containers. Another popular approach uses time-based systems, where the flow rate determines how much liquid enters the container over a set period. Advanced models incorporate sensors and computer controls to adjust for variables like viscosity, foam formation, and even container shape, ensuring consistent results every time.
Types of Liquid Filling Machines
Not all liquids are created equal, and neither are the machines that handle them. Different substances require different approaches, leading to a variety of specialized liquid filling machines:
Overflow Fillers : Ideal for thin, free-flowing liquids like water or juice, overflow fillers maintain a consistent fill level regardless of slight variations in container volume. This makes them perfect for products sold by appearance rather than weight.
Piston Fillers : Best suited for thicker liquids like sauces, creams, or oils, piston fillers use a mechanical plunger to push out exact quantities of product. Their robust design handles viscous materials with ease.
Gravity Fillers : As the name suggests, these rely on gravity to move the liquid from a holding tank into the container below. Simple yet effective, they’re often used for beverages and other low-viscosity products.
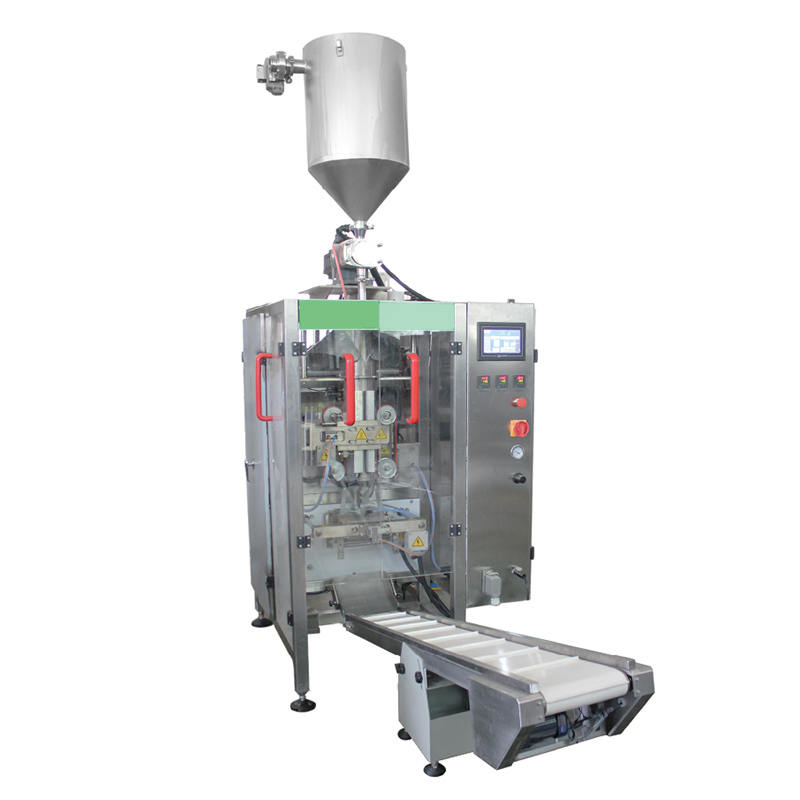
Net Weight Fillers : Common in industries where weight matters more than volume (like chemicals or detergents), net weight fillers weigh the container during filling to achieve precise measurements.
Peristaltic Pump Fillers : These gentle giants are favored in pharmaceuticals and biotech sectors because they don’t contaminate the product. By squeezing flexible tubing, they create a smooth, controlled flow without exposing the liquid to external components.
Why Are Liquid Filling Machines So Important?
Imagine trying to manually fill hundreds—or thousands—of bottles an hour. It would be slow, messy, and prone to errors. Liquid filling machines eliminate these challenges, offering several key benefits:
Speed and Efficiency : Automated systems can fill dozens of containers per minute, drastically reducing production times.
Accuracy : Precision is paramount in industries like pharmaceuticals, where even a small discrepancy could affect dosage or efficacy. Modern machines boast remarkable accuracy, minimizing waste and ensuring compliance with regulations.
Hygiene and Safety : Many machines are constructed from stainless steel and feature designs that prevent contamination. In sensitive fields like food and medicine, this ensures consumer safety while meeting strict health standards.
Flexibility : With adjustable settings and interchangeable parts, many liquid filling machines can handle multiple products, sizes, and shapes, making them versatile tools for manufacturers.
Cost Savings : While the initial investment might seem steep, the long-term savings in labor, material, and time quickly add up. Plus, reduced spillage and improved consistency mean less wasted product.
Contact Us