The evolution of fully automatic packaging machinery marks a significant turning point in the global manufacturing landscape. Today’s consumers demand high-quality products that are packaged quickly, securely, and in an environmentally responsible manner. Meeting these expectations requires more than just speed; it also requires precision and flexibility. Fully automatic packaging machinery offers all these benefits and more, making it a cornerstone of modern production lines.
One of the main driving factors behind the adoption of fully automatic packaging systems is the need for higher production volumes. As businesses scale up, manual labor becomes less efficient and harder to manage. Workers can only package a limited number of units per hour, and manual errors can lead to waste, downtime, and increased costs. Fully automatic machinery, on the other hand, operates at high speeds, capable of packaging hundreds or even thousands of units per hour without losing quality or consistency.
For example, in the food and beverage industry, where packaging is required to preserve freshness and prevent contamination, fully automatic machines ensure that the process is not only efficient but hygienic. These systems are designed to meet strict sanitation standards, which are crucial in food production. The machinery can handle tasks like filling containers, applying seals, and labeling—all in a controlled, sterile environment. This reduces the risk of contamination and ensures that products are packaged in a safe and reliable manner, ready to reach consumers in peak condition.
Sustainability is another critical factor influencing the growth of fully automatic packaging machinery. As more consumers and businesses prioritize eco-friendly practices, packaging solutions are being scrutinized for their environmental impact. Fully automatic packaging machines can be designed to work with eco-friendly materials like recyclable plastics, biodegradable films, or even paper-based packaging. Moreover, the precision of automated systems minimizes material waste during the packaging process, further contributing to environmental goals.
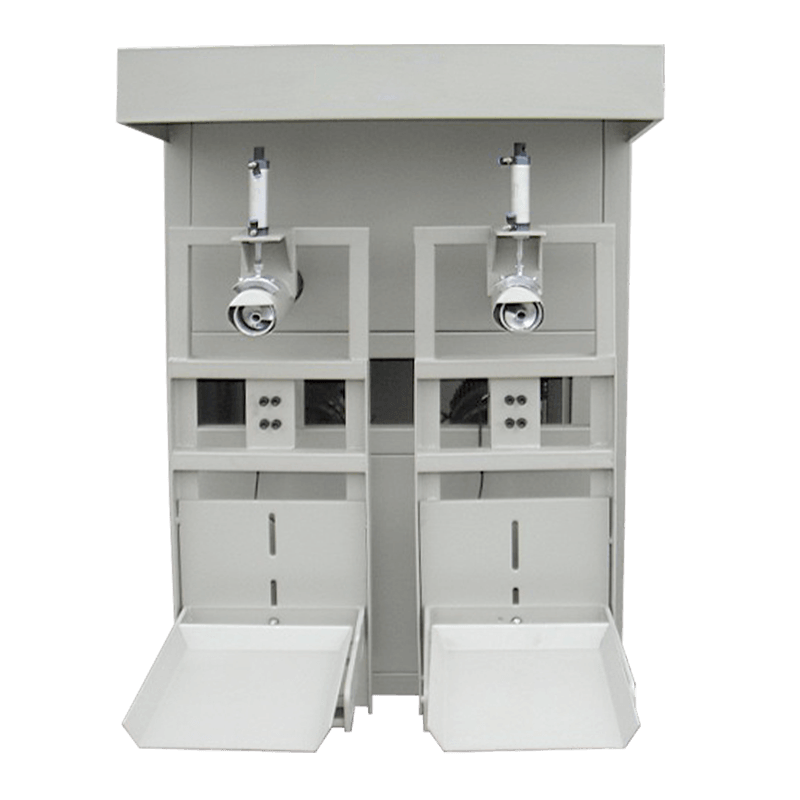
The operational flexibility of fully automatic packaging machinery is another reason for its widespread adoption. These machines are capable of adjusting to different packaging formats, sizes, and materials with minimal downtime or manual adjustments. Whether a manufacturer is packaging small sachets of product or large bottles, the system can switch seamlessly between different formats, improving efficiency and reducing lead times. This flexibility is particularly valuable in industries that produce a wide variety of products and require frequent changes in packaging specifications.
Additionally, automation in packaging enhances the traceability and accountability of production. With automated systems, manufacturers can track every unit of product from production to packaging. This is important for industries like pharmaceuticals, where regulatory compliance is stringent. Automated machines often come with integrated barcode scanners or RFID systems that help track products through the supply chain, ensuring that all packaging meets regulatory standards and can be traced back to its origin.
Finally, fully automatic packaging machinery plays a significant role in reducing operational costs. While the upfront investment in automation may be high, the long-term savings are substantial. Reduced labor costs, less material waste, and increased productivity all contribute to a higher return on investment. Furthermore, the data collected by automated systems allows businesses to identify inefficiencies in the packaging process, enabling continuous improvement and cost reductions over time.
Contact Us